Współczesny świat nieuchronnie zmierza w kierunku optymalizacji pracy wysoko wykwalifikowanych specjalistów, zapewnienia efektywności i bezpieczeństwa pracy przedsiębiorstw oraz świadomego wykorzystania rozwiązań technologicznych. W związku z tym zapotrzebowanie na stały monitoring stanu technicznego wysokonapięciowych maszyn wirujących, ze strony specjalistów technicznych w dużych przedsiębiorstwach, i elektrowniach pojawia się coraz częściej.
Z danych Electric Power Research Institute wynika, że problemy z izolacją uzwojeń stojana występują w 37% wszystkich silników elektrycznych i generatorów WN i są najczęstszą przyczyną awarii (57%), powodując największe straty i wymagając najwięcej uwagi.
Najczęstszemu problemowi, występującemu w uzwojeniach stojana silnika elektrycznego są wyładowania niezupełne. To niewielkie iskry elektryczne, które występują w uzwojeniach stojana, pracujących przy częstotliwości 50/60 Hz i napięciu znamionowym 3,3 kV lub wyższym.
Przyczyny wyładowań niezupełnych można podzielić na kilka kategorii. Defekty izolacji powstające w miejscach połączeń lub na zgięciach przewodów, tworzą mikroskopijne puste przestrzenie w materiale izolacyjnym, co prowadzi do powstania lokalnych wyładowań elektrycznych. Zanieczyszczenia takie jak kurz, wilgoć pary oleju – również odgrywają ważną rolę, tworząc przewodzące ścieżki dla wyładowań i zmniejszając wytrzymałość elektryczną izolacji. Wilgoć sprzyja jonizacji powietrza, co zwiększa prawdopodobieństwo wyładowań przy niższych napięciach. Z czasem materiały izolacyjne tracą swoje właściwości z powodu starzenia cieplnego i naprężeń mechanicznych, co prowadzi do mikropęknięć i zwiększa prawdopodobieństwo wyładowań. Uszkodzenia mechaniczne, spowodowane m. in. wibracjami, mogą również uszkodzić izolację i powodować występowanie wyładowań niezupełnych.
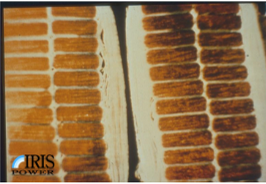
Rys. 1. Uszkodzenie izolacji uzwojeń stojana
Pomiary wyładowań niezupełnych wymaga zastosowania specjalistycznego sprzętu, który najczęściej składa się z trzech elementów: czujników wykrywających wyładowania niezupełne, systemu szybkiego reagowania na zmiany stanu maszyny oraz prognozowania jej dalszej pracy. Wysokoczułe czujniki, zainstalowane w kluczowych punktach silnika, diagnozują wyładowania niezupełne na zasadzie rejestracji fal elektromagnetycznych, co pozwala wykrywać wyładowania na wczesnym etapie. Systemy monitoringu on-line zbierają dane w trybie rzeczywistym i przekazują je do centrum przetwarzania danych w celu analizy i diagnostyki. Oprogramowanie wykorzystuje algorytmy uczenia maszynowego i modelowania do przewidywania przyszłych awarii i optymalizacji planów konserwacji.

Rys. 2. Etapy monitoringu wyładowań niezupełnych
Monitoring w czasie rzeczywistym można porównać do pracy mózgu gadziego, układu limbicznego i neokorteksu u człowieka. Mózg gadzi odpowiada za instynkty przetrwania i natychmiastowe reakcje, analogicznie do tego, jak czujniki monitoringu rejestrują anomalie. Układ limbiczny zarządza emocjami i pamięcią długotrwałą, co można porównać do systemów analizy danych, które przetwarzają i przechowują informacje o stanie sprzętu. Neokorteks, pełniący funkcje wyższego myślenia i prognozowania, jest podobny do oprogramowania systemu monitoringu, które używa algorytmów uczenia maszynowego do modelowania planu pracy i grafików wyłączeń maszyny w prognozowanej przyszłości.
Monitoring wyładowań niezupełnych jest ważny z kilku powodów. Wczesne wykrycie problemów i zapobieganie poważnym awariom pozwala planować prace naprawcze, co zmniejsza koszty nieplanowanych napraw i wymiany drogich komponentów. Zmniejszenie ryzyka sytuacji awaryjnych zwiększa bezpieczeństwo personelu. Niezaplanowane awarie mogą prowadzić do wypadków, zagrażających życiu i zdrowiu pracowników, dlatego terminowy monitoring zmniejsza te ryzyka. Niezawodna praca sprzętu gwarantuje nieprzerwaną produkcję i realizację planów produkcyjnych, co jest szczególnie ważne dla dużych przedsiębiorstw przemysłowych i elektrowni.
Jednym ze światowych liderów w dziedzinie monitoringu stanu układów izolacyjnych wysokonapięciowych maszyn wirujących jest kanadyjska firma IRIS Power – A Qualitrol Company, założona w 1990 r. Obecnie sprzęt IRIS Power jest zainstalowany na ponad 19 tysiącach generatorów i silników elektrycznych na całym świecie, również w Polsce. Przez ostatnie 32 lata firma sprzedawała jeden przyrząd do monitoringu częściowych wyładowań i 12 zestawów czujników każdego dnia roboczego.
Technologia stosowana przez firmę IRIS Power pozwala skutecznie oddzielać szumy i zakłócenia od rzeczywistych sygnałów wyładowań niezupełnych. Zgodnie z zaleceniami międzynarodowego standardu IEEE 1434-2000 (IEEE Guide to the Measurement of Partial Discharges in Rotating Machinery), czujniki zaprojektowane przez firmę IRIS Power mierzą maksymalną amplitudę dodatnich i ujemnych impulsów wyładowań niezupełnych na poziomie częstotliwości powtarzania 10 imp/sek (parametr ±Qmax) i obliczają całkowitą aktywność wyładowań (parametr ±NQN – Normalized Quantity Number). Ponadto, urządzenia analizują położenie impulsów wyładowań względem fazy napięcia 50/60 Hz. Wyniki pomiarów są przetwarzane za pomocą oprogramowania PDView i prezentowane w postaci wykresów i tabel w dwóch- i trójwymiarowych wizualizacjach.
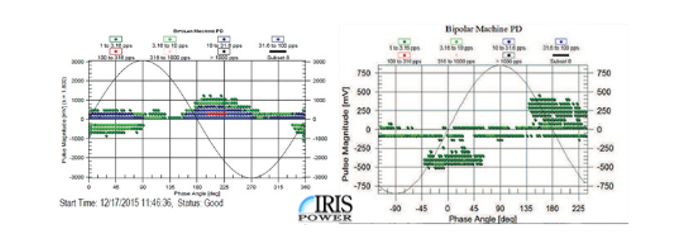
Rys. 3. Dane, uzyskane za pomocą monitoringu IRIS Power
Baza danych IRIS jest największą bazą danych tego typu na świecie i zawiera ponad 750 tysięcy wyników pomiarów wyładowań niezupełnych. Wyniki uzyskano przy użyciu sprzętu firmy IRIS podczas testowania generatorów i silników elektrycznych różnej klasy napięcia i mocy, różnych producentów w różnych regionach świata. Baza danych zawiera pełne informacje o parametrach każdej maszyny elektrycznej, na której przeprowadzono pomiary wyładowań niezupełnych, firmie-producenta, metodzie chłodzenia, klasie napięcia, użytych czujnikach (EMC lub SSC) oraz wynikach testów.
Wczesne wykrycie wyładowań pozwala uniknąć poważnych uszkodzeń i przeprowadzać minimalnie inwazyjne prace naprawcze, co wydłuża żywotność sprzętu i obniża koszty kapitałowe remontów. Ciągły monitoring poprawia ogólną niezawodność i bezpieczeństwo pracy sprzętu, a kontrola on-line stanu izolacji i innych krytycznych parametrów pozwala utrzymywać sprzęt w optymalnym stanie, co minimalizuje ryzyko awarii.
Podsumowując, możemy powiedzieć, że teraz łatwiej jest optymalizować i prognozować pracę wysokowoltowych maszyn wirujących. Wczesne wykrycie najczęściej występującego problemu – wyładowań niezupełnych – pozwala uniknąć poważnych uszkodzeń i przeprowadzać minimalnie inwazyjne prace naprawcze. Ciągły monitoring poprawia ogólną niezawodność i bezpieczeństwo pracy sprzętu, a kontrola online stanu izolacji i innych krytycznych parametrów pozwala utrzymywać sprzęt w optymalnym stanie, co minimalizuje ryzyko awarii.
Autor: Oksana Krupka, Menedżer Produktów IRIS Power Zakład Usług Technicznych Energoaudyt sp. z o.o.
Źródło: Zakład Usług Technicznych Energoaudyt sp. z o.o.
Artykuł sponsorowany (artykuł z wydania 4/2024 “Nowa Energia”)